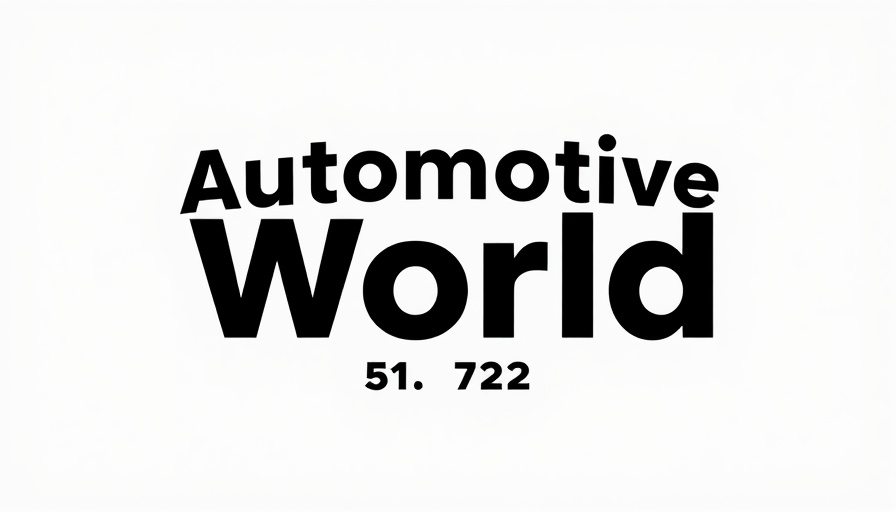
Revolutionizing Battery Recycling: A Shared Path to Sustainability
In a landmark collaboration that could reshape the electric vehicle (EV) battery supply chain, Panasonic Energy and Sumitomo Metal Mining are embarking on a groundbreaking recycling initiative for nickel used in lithium-ion batteries. Scheduled to launch in 2025, this initiative represents the first-ever closed-loop recycling process within the automotive battery production sector, setting a new standard for sustainability.
Understanding Closed-Loop Recycling
Closed-loop recycling, where the end-of-life products are reprocessed into raw materials for the same type of product, is increasingly vital. This initiative aims to reclaim and reuse nickel from battery scraps generated in Panasonic's Osaka factory. Consequently, this recycled nickel will be transformed back into cathode materials, integrating seamlessly into new lithium-ion batteries. As Panasonic Energy's CEO, Kazuo Tadanobu, states, “Building a sustainable recycling scheme for end-of-life lithium-ion batteries is crucial for the future expansion of EVs.”
Broader Implications for the EV Market
With the expected peak in automotive batteries reaching their end-of-life around 2030, the collaboration underscores an urgent need for a robust recycling system. By efficiently reclaiming metals like nickel, cobalt, and lithium from spent batteries, stakeholders can ensure that the demand for these rare materials is met sustainably. This approach also aligns with the increasing pressures on manufacturers to reduce their carbon footprints amidst a global push for climate-conscious practices.
Future Plans: Expanding Beyond Nickel
Initially focused on nickel recovery, Panasonic and Sumitomo plan to broaden their efforts to include lithium and cobalt by 2026. This expansion is not just about increasing the percentage of recycled materials; it is about laying the foundation for a sustainable ecosystem where every component of battery production can be reused, ultimately reducing CO₂ emissions significantly compared to traditional mining methods. Panasonic aims for 20% recycled cathode material in its automotive batteries by 2030.
The Economic Landscape of Recycling
As the electrification of vehicles accelerates, opportunities for efficient recycling practices can drive down costs. Efficient recovery of precious metal resources can also enhance job creation in the recycling and manufacturing sectors. Additionally, as battery technology evolves, the materials market could experience less volatility, stabilizing used car financing rates. This provides a compelling argument not only for environmental sustainability but also for economic resilience.
Practical Takeaways for Dealerships
For dealership principals and GMs, understanding this evolving landscape of battery recycling and sustainability trends is crucial. Integrating these practices could not only appeal to an increasingly eco-conscious clientele but potentially influence the financial dynamics of used car financing. Staying informed about these developments can position dealerships favorably as partners in these initiatives or as advocates for sustainable automotive practices.
The automotive industry stands at a crossroads where sustainability meets innovation. As manufacturers like Panasonic Energy set a precedent for responsible materials management, dealerships can stay ahead by considering the implications for used car financing rates and embracing the transition to more sustainable, circular practices. By doing so, they can contribute positively towards an environmentally sound future while enhancing their business resilience.
Write A Comment